R&D organisation Offshore Renewable Energy (ORE) Catapult last year began a project with offshore wind turbine manufacturer GE to develop remote maintenance systems through robotics and automation.
Engineering Manager at ORE Catapult Tony Fong is appearing at the SOE Symposium to talk about the cost-cutting programme. He is joined by Head of Communications Lee Madigan to tell us how fixed plant operation and maintenance jobs are set to change, and how the UK is embracing automation technology.
Symposium
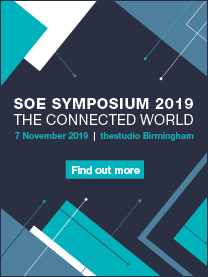
When speaking at the SOE Symposium in November, what will you be telling the audience?
Tony Fong (TF): I will be giving a general overview of the offshore wind market. The reasons why they are looking for innovations around wind farm maintenance and how robotics fit into that roadmap. It’s seen as not only good to have for the industry, but it’s also one of the vital areas of cost reduction.
What is it about this project that operations engineers can learn from?
TF: The main aspect, in terms of an operationally focused project, is how we see plant operation changing in the future; so, we are moving from an operations procedure where everything is done by humans to a different model; a move towards more automated, robotic and digital operations and maintenance procedures – this can be done offshore and can make remote operation possible. All offshore wind farm owner/operators are looking at how they can decrease the amount of offshore activity, not only from a health and safety perspective, but also from a cost perspective. We’ll explore how we see that progressing in the future.

Do you think events such as the Symposium help in generating debate about connectivity and digitisation?
TF: One of the big challenges that we do come across is the perception that robots and digitisation will decrease the amount of jobs; I don’t think that will be the case. With offshore wind being an example, it’s an absolute booming industry now - or it will be very soon - with current trends of growth in the sector; we just can’t keep up in the skills market. So, the move to robotics and automation is necessary to support that growth. It’s not replacing jobs; it’s changing what the future operations jobs will look like.
Do you believe engineers are generally receptive to the potential from mass data and connectivity?
TF: I think that depends on the industry you’re in. I was at an Unmanned Aerial Vehicle (UAV) event last week for the oil and gas sector – it’s interesting the difference in reception you get talking about new technologies, such as digital or mass data, in that industry compared to similar sessions I’ve been to in offshore wind. It’s a very new industry which is still forming, and there’s no set way of doing things, so they’re quite receptive to change. If you go to an industry such as oil and gas, which has decades of processes, procedures and a very different risk profile, it’s harder to make that change.
Project
How big is the potential for offshore wind in the UK, benefiting from industry and academic collaborations?
Lee Madigan (LM): Offshore wind is a very new industry; it only started in the early 90s, so we’ve seen huge growth since the first windfarm was installed off the coast of Blyth in 1991 – it’s only just been decommissioned. From zero to almost 9GW installed in the UK waters alone, and the recently announced Offshore Wind Sector Deal, which sets out the industry’s ambition for the next ten years, is looking at a minimum of 30GW of installed capacity by 2030 – enough to generate a third of the country’s electricity needs. The recently announced Committee on Climate Change report is recommending ‘net zero’ by 2050 – so they’re looking at 75GW of offshore wind in the UK alone by 2050 to meet those needs. So, as a relatively new industry, we’ve seen massive growth and that’s only going to continue. It must do to continue to meet the clean energy generation needs of the UK going forward.
We believe that 30GW by 2030 is achievable. We’ve already got plenty of planning in the pipeline – 75GW is possible if we embrace new technologies, such as robotics, digitisation, AI – and look at new innovations and technologies such as floating wind, for example. We believe they are achievable and necessary.
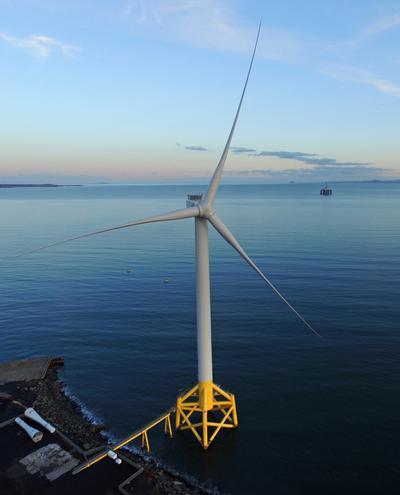
How important is the implementation of robotics and automation on cost reduction?
TF: We’ve done some studies ourselves, and have looked at results from independent studies, which show that about 20% of the cost of energy in offshore wind is within operations and maintenance. A big portion of that is associated with vessel time, turbine downtime and offshore personnel – that’s around 10% – so the portion of doing physical activities offshore is a big slice of the pie. Even if you can reduce half of it through robotics and automation, that would be a 5% reduction to the cost of energy, which is substantial.
Do you think the government are giving enough support for the offshore wind sector?
LM: I think so. The sector deal that was announced in March was a joint industry UK government commitment. The UK government has been very supportive of offshore wind and going forward, the sector deal shows what the industry can achieve with the correct level of government support. So, the UK government sees offshore wind as a key part of its climate change commitments going forward.
Do you think the UK has been fast enough / as fast as other European countries to adopt automation technology?
TF: In offshore wind, the UK is very much leading the way. We’ve got the most installed offshore capacity; certainly, within operations and maintenance phase. We’ve got big owners and operators looking at some quite adventurous automation technology; I don’t believe in offshore wind that we’re behind on the robotics front.
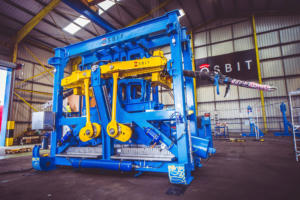
LM: Certainly, robotics and AI is one of the key grand challenges in the government’s industrial strategy, so the government see the UK as having a real competitive advantage in that area and are keen to build on that and make a strong UK economic benefit. We would then look to export that expertise and the products and services worldwide. The UK is committed to developing the robotics and AI economy.
How important is the £1.5m programme to test and demonstrate new technologies?
LM: Vattenfall’s European Offshore Wind Demonstration Centre (EOWDC) off Aberdeen is a really cutting-edge development. It’s a demonstration site, and one of the key barriers for small companies trying to bring new innovations to market is finding somewhere where they can test, demonstrate and validate those new technologies in a real-world environment, because a lot of working wind farms don’t want to take the risk on. The beauty of our partnership with Vattenfall is that we can work with these small companies to identify what the most promising technologies are and take them through an incubator-type approach programme where we can help them develop. We have our own turbine just off the coast of Fife which we use a lot to help small companies to develop their technology. Then, when we’re confident and comfortable with that technology, we can introduce them to companies such as Vattenfall and allow them to test and demonstrate their technology in a real-world environment. That helps to reduce risk, it helps with investor confidence and it helps to bring these technologies to commercialisation much faster.
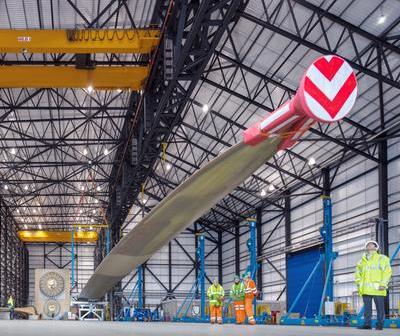
How receptive is industry to robotic maintenance?
TF: I would say that most of them have already bought into it, but some are just trying to find their feet on how they want to use it. So, the likes of GE, which, in collaboration with ORE Catapult, is developing a programme called ‘stay ashore’, is looking at how you design a turbine in a way that reduces the maintenance requirements offshore, so I think they are already bought in. What we’re doing at Catapult is bringing the added technologies to allow them to achieve their goals.
A lot of the big manufacturers and equipment operators don’t necessarily have the time to scour the supply chain and look for those technologies, so if we’re able to present and bring those technologies to them - proved, tested, commercialised - then it’s much easier for them to invest because that risk has been reduced. So, it helps them to move that supply chain support along a lot faster.
CPD
Other than internally, how do you keep learning about the technology and the sector?
TF: I do attend quite a lot of events. I present at quite a few events too, which counts towards my CPD. Attending industry conferences, such as global offshore wind a few weeks ago, is a good way to speak to others first-hand, and to a lot of the small companies.
One key method of keeping up is through Catapult’s contact with stakeholders. Much of our day-to-day job is going out and speaking to people about their everyday challenges and that’s where I get most of my knowledge; that daily contact with people, many of whom are from outside of my company.
The SOE Symposium takes place on 7 November 2019 at thestudio, Birmingham.
Book your place